12
2025
-
06
钎头一次成型工艺及模具设计
介绍了钎头温挤成型工艺的研制过程、主要工艺参数的确定及模具设计过程。
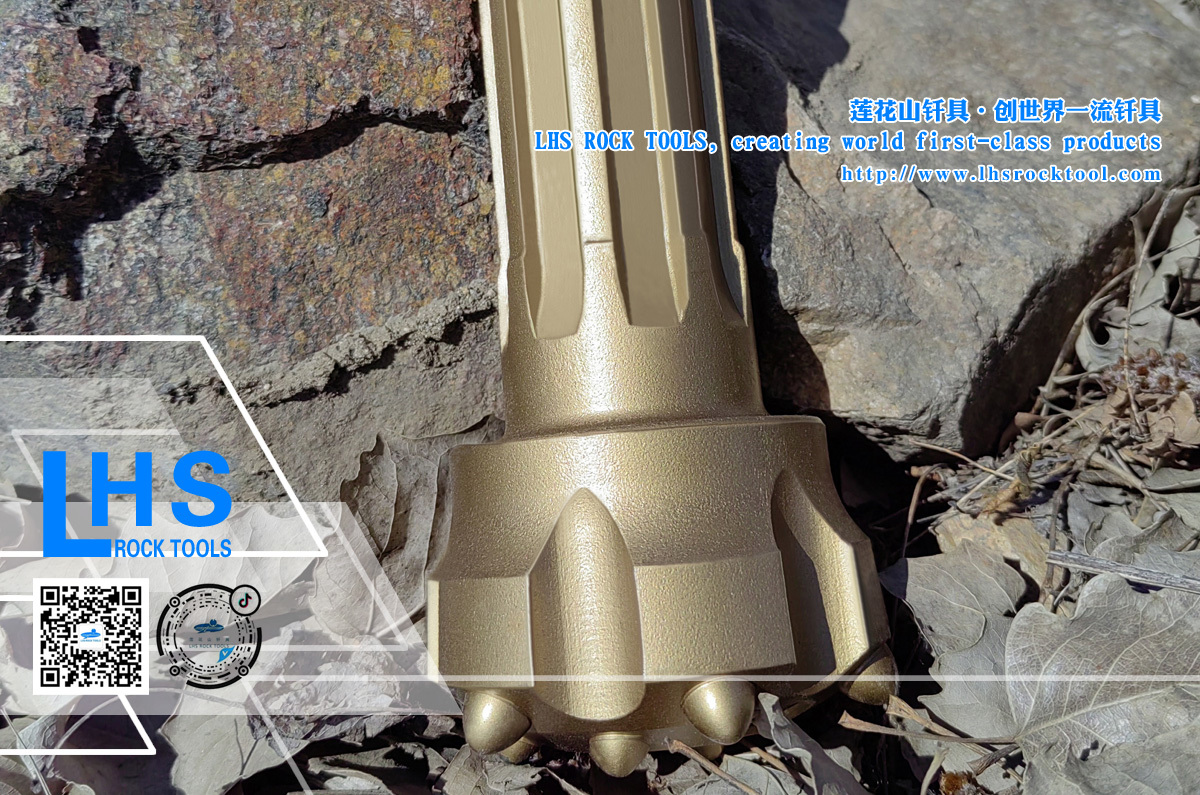
图1所示钎头是钻探设备中的核心零件,由于工作环境恶劣、损耗大、用量多,是钎具行业量大面广的产品。现在钎头的生产主要是采用圆形棒材经车、铣等切削工艺加工成形,因其外形复杂,机加工难度大,材料利用率低,导致生产成本居高不下。另外金属内部的纤维组织因车、铣削而裸露,降低了零件的耐疲劳强度。针对以上问题,本文提出了一种新的成型方法--温挤成型。不仅可以提高生产效率和材料利用率,降低生产成本,还可提高零件的强度。
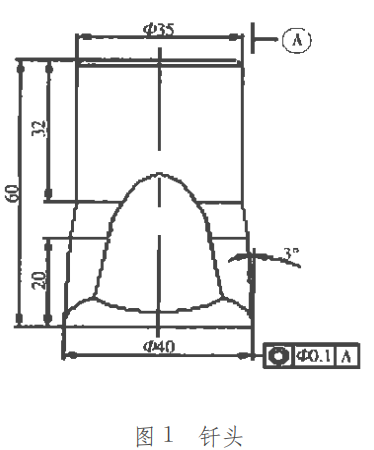
1. 工艺分析
挤压是一种先进的无切削加工工艺,根据成型温度不同可分为冷挤、温挤和热挤。冷挤时,零件精度高,但变形抗力大且必须采用后续退火工艺;热挤可降低变形抗力,但零件的表面质量和尺寸精度下降。温挤成形是将毛坏加热到室温以上,再结晶温度以下的某个适当温度进行挤压,其特点是成型压力低,尺寸精度接近或相当于冷挤零件,且可连续生产。故利用温挤成型来生产钎头,可避免冷、热挤压及车,铣削成型的不足,主要表现在:
(1)金属材料的温挤成型,可隆低变形抗力,从而降低设备吨位,减轻模具的负荷。
(2)温挤成型时,金属组织不发生相变,也没有过度的加工硬化,工件表面氧化极微,有与冷挤相当的尺寸精度,但无须后续退火工艺,且纤维流线沿轮连续分布,有利于提高零件的耐疲劳强度。
(3)温挤压成形可采用压力机连续生产,效率数十倍于车、铣削工艺。
2.工艺过程及工艺参数的确定
2.1确定工艺路线
为了减少变形程度、降低变形抗力,应采用与钎头圆柱部分直径相同的圆形棒料作为毛坏,坏料长度根据零件的体积确定。另外,为了提高凸模成型时的稳定性,坯料的一端应加工与凸模弧面相同的凹坑(见图2)。钎头温挤成型工艺流程如图3所示。
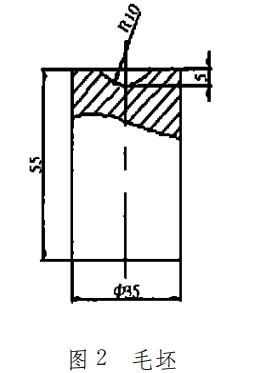
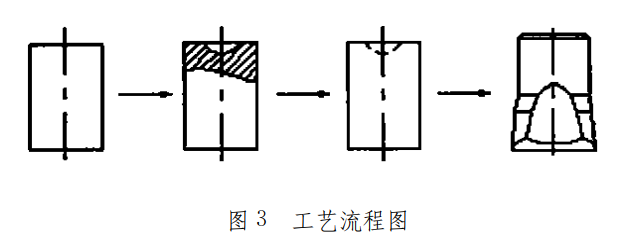
2.2确定成型温度
一般认为温挤成型中坯料加热温度要求在室温以上,工件材料的再结品温度以下。具体确定成型温度时,应考虑成形力、工件精度和模具寿命等因素。成形温度越低,表面氧化少,工件精度高,但变形抗力大,设备吨位和模具负荷增加;成形温度越高,变形抗力下降,有利于工件的成形,但表面氧化严重,工件精度也随之下降。
钎头的材料为40Cr钢,从保证工件的精度要求和延长模具使用寿命等方面考虑,在坏料表面不发生严重氧化和内部金相组织不发生相变的前提下,应尽可能提高加热温度,以降低成型压力。在实验中,采用2500Hz,100KW的中频感应电炉加热,当加热到 750℃时,坏料镦粗后基本没有氧化皮脱落;当加热到850℃时,镦粗后仅有很薄的一层氧化皮脱落;当加热到950℃时,坯料表面氧化严重,镦粗后,可发现有较多的氧化皮脱落。另外, 40cr钢在正挤成型、变形程度为60%的条件下,坏料温度700℃时,其变形抗力为1100MPa;当坏料温度提高到850℃时,其变形抗力为690MPa,下降了38%。故从提高工件精度和延长模具使用寿命来考虑,坯料的加热温度确定为:850℃+50℃。
2.3润滑剂的选择
温挤成型能否顺利进行与坯料的润滑是否合理有直接的关系。因为良好的润滑能降低变形抗力、降低设备吨位、减少模具的磨损,提高工件的表面质量。温挤成型润滑剂首先应具有足够的热稳定性,即在成型温度下仍能保持良好的润滑效果。其次应具有良好的粘附性,在一定温度下能均匀粘附在坯料或型腔的表面,不堆积成厚的薄膜。
目前,温挤成型所用的润滑剂种类较多,有的在热态下工作性能下降,有的润滑效果好,但使用不方便。通过多次试验比较,以二硫化钼油剂、玻璃粉、硼砂等为主要成份的润滑剂,在成型前均匀地涂涮在凸模和型腔表面,可以取得较好的润滑效果。一般情况下,模具的使用寿命可达1万件左右。
3. 模具设计
3.1模具结构设计
因为钎头的形状为上小下大,为了脱模方便,凹模采用哈夫分型结构,模具结构如图4所示,工作过程如下;
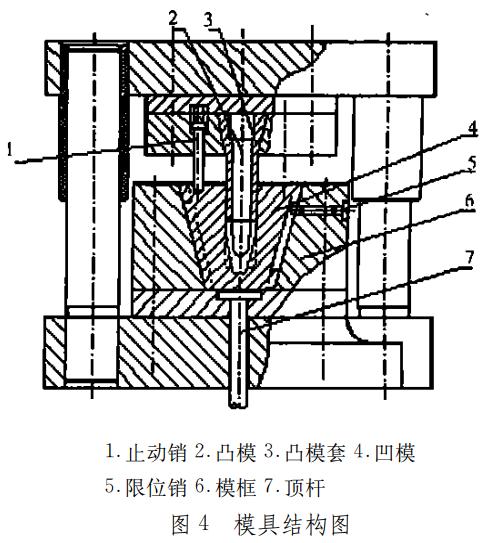
模具在开启位置时,将加热到预定温度的毛坏置入凹模型腔,由型腔的园柱面定位。然后液压机横梁下行,凸模进入型腔,还料金属在凸模的压力下发生塑性变形,并充满型腔。成形结束后,液压机横梁上行,凸模离开型腔,启动液压机的顶出油缸,顶出油缸的顶出力通过顶杆作用在凹模上使凹模向上运动;同时,凹模受模框T形槽的限制,产生横向开模动作,当开模宽度大于工件的最大直径后,工件即可卸下。
3.2 模具主要工作零件的设计
3.2.1 凹模锥度α的确定
在哈夫分型结构中,凹模拼块与模框采用锥面配合,其锥度《的选择很重要。成型时凹模拼块受力如图5所示,P--成型时金属坯料作用在凹模拼块上的胀模力,N--模框作用在拼块上的正压力,F--摩擦力。把胀模力P进行分解,平行于配合面的分力P1=Psinα,垂直于配合面的分力P2=Pcosα。
在垂直于配合面的方向:N-P2=0,N=P2=Pcosα。
在平行于配合面的方向:P1=Psinα,F=f·N=f·Pcosα。当α增加,P1增加,F减小,凹模拼块容易上浮,哈夫模分开,产生飞边,工件尺寸也会发生变化。如果是圆锥形凹模,上浮后,凹模与模框之间的面接触变成线接触,凹模拼块在胀模力产生的弯矩作用下极易扳裂,这是圆锥形凹模失效的主要原因。因此,从凹模受力来考虑,锥角α不能取得太大。
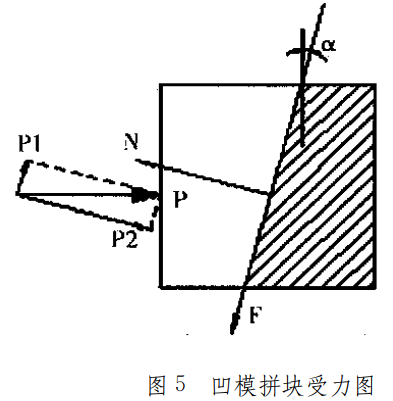
另一方面,凹模拼块的开模距离S与顶出行程日的关系如图6所示。顶出行程H-S/tgα,(开模距离S只与工件直径有关)上式中,α越小,顶出行程 日越大,凹模与模框的配合长度减少,顶出时容易造成凹模拼块失稳而倾翻。因此,从凹模顶出来考虑,锥角α不能取得太小。
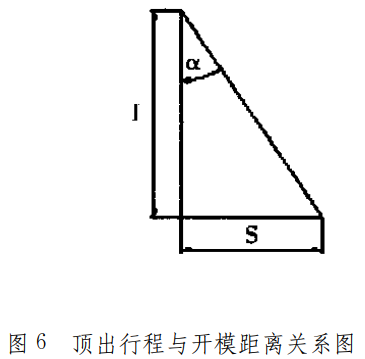
经多次分析与实验,锥角α取15°左右时,获得了满意的效果。
3.2.2 止动装置的设计
成型结束后,凸模上行时,如果工件对凸模的包紧力较大就会把凹模拼块提起来,凹模自动分型,工件就包在凸模上不能分开。为了克服这一缺点,需要在模具上设计凹模止动装置,如图7所示。凸模上行时,两止动销限制了凹模拼块的横向开模动作,加上T形槽的作用,型腔就无法向上运动,这样凸模与工件就能有效分开,然后利用顶出装置把工件从型腔中顶出。
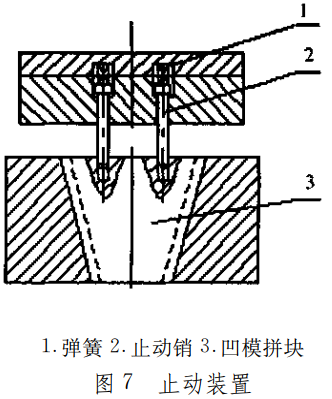
4.结束语
由上述的研究分析和实验可知,钎头由原来的车、铣削成型工艺改为温挤成型,不仅在技术上是可行的,通过实验已得到了合格的产品,而且在经济上也有十分可观的效益,生产效率和材料利用率得到了显著提高。因此,温挤成型作为一种少无切削成型的新工艺,对于成型精度高、形状复杂的零件具有普遍的使用和推广价值。
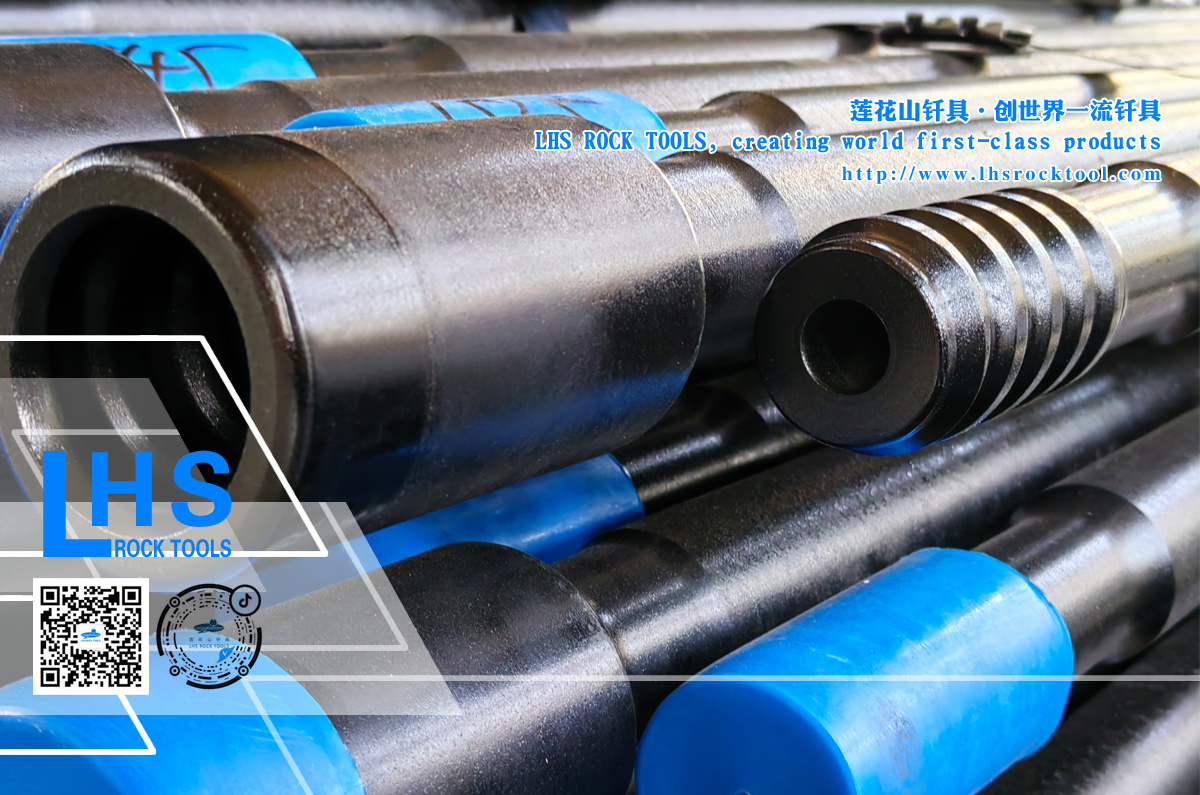
上一篇
下一篇
上一篇
下一篇
相关资讯
暂无数据